2019 Associated Masonry Contractors of Houston Golden Trowel Honor Award
- Camarata Masonry
- Dec 18, 2019
- 3 min read
Project: TMC Highrise (Latitude Apartments)
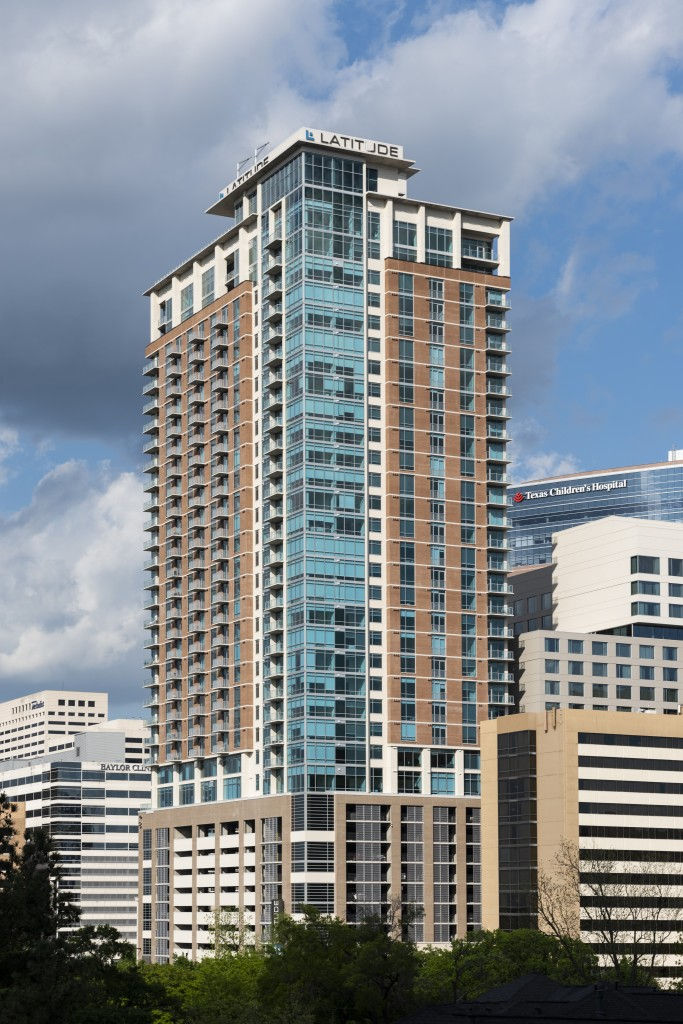
>>> TMC Highrise, now known as Latitude Medical Center Apartments is a 34 story, 615,000 square foot, luxury apartment high rise nestled in the Texas Medical Center, Rice District, and Hermann Park area. This upscale tower provides residents with amenities such as a rooftop pool, a sky lounge, a fitness center, 24-hour front desk service, concierge, and valet parking.
Camarata Masonry Systems, Ltd. (CMS) was responsible for the exterior masonry veneer and interior CMU walls on this project. The façade of the tower portion utilizes Canyon Brown modular brick accented with white mortar and solid Canyon Brown modular brick on the window sills. Slate Grey modular brick is used on the garage level and regular lightweight 8” and 12” CMU is used for the partition walls in the garage. The mechanical rooms, stair walls and elevator walls are constructed with 8” and 12” 4-hour rated CMU. The main entrance is highlighted by the use of 1 3/8” thick pieces of 1’ x 2’ cast stone. The construction of this project required both conventional scaffold and a multi-point suspended scaffold system for upper areas where the use of conventional scaffold became impractical. The suspended scaffold was hung from 7 x 7 beams that projected out several levels above so that the prepping trades could work off of the top level of the scaffold to prepare an area then be raised so that we could install brick on the newly prepared area while the prepping trades continued working above. During the assembly of the conventional scaffold at the northwest corner of the building it was discovered that placement the temporary power transformer post and electrical panel would not allow enough distance between the equipment and the conventional scaffold for safe use of the scaffold. Our Safety Director was contacted to help devise an alternate plan for continuing our work and avoiding a delay on the project. The final plan was to use a 2’ swing stage that wrapped 18’ around the north face of the building and 8’ along the west face. To meet OSHA regulations for maintaining a safe working distance from the transformers and nearby powerlines, CMS used the 2’ swing stage scaffold to begin laying the exterior brick at the 4th level, continuing to the 10th level. Prior to the installation in this area, all employees were required to attend several meetings where they were reminded of the hazards, regulations and importance of safe work near electrical equipment and lines. When the temporary power was removed CMS returned to the area to erect the conventional scaffolding that was used to install the precast on the 1st and 2nd level as well as the brick on the 3rd level.
One of the unique requirements on this project involved the rebar placement in the CMU walls of the parking garage. Usually CMU wall partitions use typical rebar reinforcing spacing and sizes. On this project different parameters had to be considered for the CMU that were installed in the parking garage. Parking garages are open pathways that allow wind to come through the ramps which can create a wind cyclone effect. Different rebar spacing and sizes had to be specified based on the wind load that was going to be imposed on the various locations of these partitions. CMS provided rebar shop drawings for the engineer of record to review to ensure that the CMU walls could withstand the wind cyclone effect. Because the final drawings were atypical, the onsite foreman and lead man had to be very diligent when the walls were being laid out and built so that each CMU wall had the proper rebar size and spacing. On time deliveries had to be thoroughly coordinated because of the project’s location and because the jobsite delivery access was shared with the new Greystar Hotel that was being constructed next door.
Before CMS mobilized, our Project Manager participated in LEAN meetings to go over safety, efficiency, critical path items, logistics, and coordination with other trades, which would benefit the final job completion date. The project was a success and a large portion of this was due to the multiple coordination meetings held by both the general contractor and the subcontractors. The ability to meet with each other and modify the plan as needed was critical to maintain a continuous work flow with limited work stoppage. In turn, this allowed the project to be completed timely and to fit the needs of the growing community.